The Essential Guide to Top Welding Supplies for Every Project
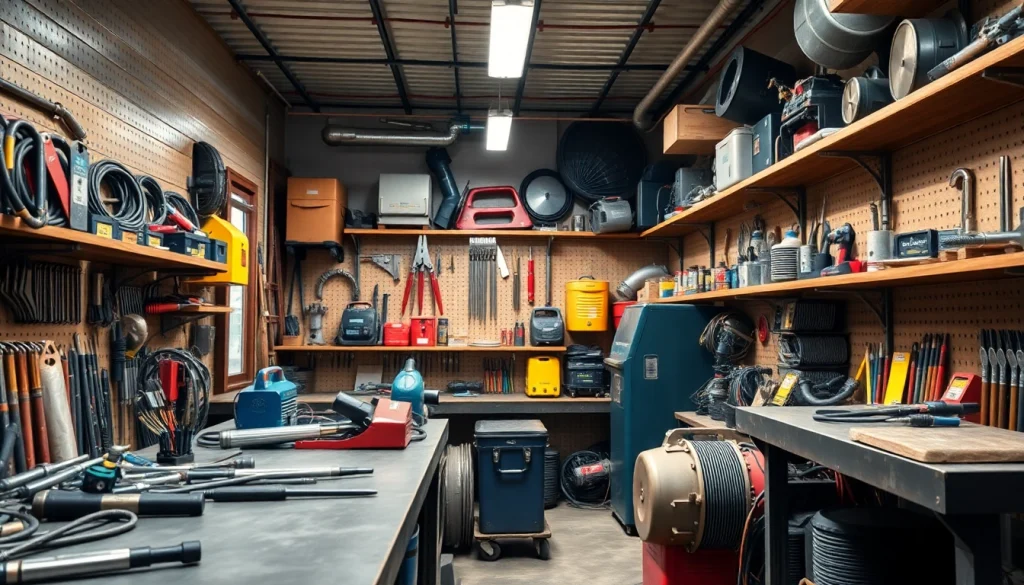
Understanding Welding Supplies
In the world of fabrication and repair, welding supplies are the backbone of every project. Whether you’re a hobbyist pursuing metal art or a professional in the construction industry, the right tools and supplies are pivotal to success. This comprehensive guide explores the essentials of welding supplies, safety gear, purchasing practices, best usage tips, and the latest trends in the welding market.
What Are the Essential Welding Supplies?
Welding supplies encompass a range of tools, equipment, and materials required for different welding types and applications. At the core of these supplies are:
- Welding Machines: Different types include MIG welders, TIG welders, Stick welders, and multi-process machines, each designed for specific applications.
- Electrodes and Filler Materials: For producing welds, these materials are crucial in varying the welding technique and achieving desired weld quality.
- Protective Gear: Safety equipment such as helmets, gloves, and aprons to protect welders from hazards.
- Welding Accessories: These can include clamps, welding carts, and spanner sets that facilitate the welding process.
- Cleaning Tools: Wire brushes and grinders used for surface preparation and cleaning after welding.
- Gas Supplies: For gas welding, oxygen and acetylene tanks are critical components.
Each category of supplies plays a significant role in ensuring the weld quality and safety of the welder.
Different Types of Welding Equipment
Welding equipment can vary significantly based on the process being utilized. Understanding these differences is key to selecting the right equipment for a project.
- MIG Welding Equipment: Known for its speed and ease of use, this equipment uses a continuous wire feed to create welds, making it ideal for thicker materials.
- TIG Welding Equipment: Suitable for thin materials and precise work, it utilizes a non-consumable tungsten electrode and offers greater control over the welding process.
- Stick Welding Equipment: This more versatile method works well in outdoor conditions and for thicker materials requiring strength.
- Plasma Cutters: Essential for cutting metals, they utilize a high-velocity jet of ionized gas.
- Spot Welders: These are used for sheet metal applications where electrical resistance is employed to create localized heat that fuses materials together.
- Multi-Process Welders: These versatile machines can handle multiple types of welding processes, offering flexibility for various projects.
Choosing the right equipment is crucial for achieving the best results based on the project requirements.
Choosing the Right Welding Supplies for Your Needs
Selecting the appropriate welding supplies requires a clear understanding of one’s projects, including the materials to be welded, the welding method to be employed, and the desired outcome. Here are key factors to consider:
- Type of Metal: Different metals require specific welding techniques. For example, aluminum welding generally necessitates a TIG set-up, while steel can be welded using MIG.
- Thickness of the Material: This determines the welding technique and equipment needed. Thicker materials might require stick welding for stronger joints.
- Environment: If welding outdoors, consider wind flow and whether the chosen method and supplies are suitable for the conditions.
- Experience Level: Some welding methods are more complex than others. Beginners might start with MIG welding due to its user-friendly nature, while professionals may opt for TIG for detail-oriented projects.
- Budget: High-quality supplies can demand a higher investment, but they often provide better durability and results in the long run. Evaluating long-term needs can justify initial costs.
Understanding these factors ensures welders invest in supplies that effectively meet their project requirements.
Safety Gear for Welders
Welding is a hazardous profession, involving exposure to extreme temperatures, dangerous fumes, and potential injuries. Therefore, the adoption of appropriate safety gear is essential.
Importance of Protective Equipment
Protective equipment reduces the risk of accidents and health issues in the workplace. Essential aspects include:
- Eye Protection: Welding helmets with proper lens shade significantly reduce exposure to ultraviolet and infrared rays.
- Skin Protection: Welding jackets, gloves, and safety shoes prevent burns and injuries from hot sparks.
- Respiratory Protection: Respirators or masks should be used to avoid exposure to harmful fumes and particles.
- Hearing Protection: In high-decibel environments, earplugs or earmuffs should be used to prevent hearing damage.
Investing in high-quality protective equipment is necessary for maintaining safety over time.
Recommended Welding Safety Gear
Some popular welding safety gear includes:
- Welding Helmets: Opt for auto-darkening helmets that adjust the lens shade automatically to ensure maximum visibility and safety.
- Welding Gloves: Choose gloves with heat-resistant materials and ergonomic design for better grip and dexterity while welding.
- Welding Jackets: Leather or flame-resistant fabric jackets serve as effective barriers against sparks and heat.
- Respirators: Use half-mask respirators with P100 filters for maximum protection against fine particles and fumes.
Ensuring safety gear meets industry standards can greatly reduce the risk of injuries.
Maintaining Your Safety Equipment
Regular maintenance of safety gear prolongs its effectiveness and durability. Best practices include:
- Regular Inspections: Check for damages like tears in gloves or visors and replace as necessary.
- Cleaning: Ensure helmets are clean and lenses are free from dust to maintain visibility.
- Storage: Safeguard safety gear in dry, cool areas to prevent premature wear due to environmental factors.
- Adhering to Expiry Dates: Some items like gas filters and certain gloves come with expiration dates and should not be used beyond these limits.
Proper upkeep of safety gear is an often-overlooked aspect of maintaining a safe working environment.
Buying Welding Supplies Online
The digital age has transformed how welders acquire their supplies, allowing them to access a wide variety of options from the comfort of home. However, navigating this space requires some knowledge.
Top Online Retailers for Welding Supplies
Some of the leading online retailers offering a vast selection of welding supplies include:
- Cyberweld: Known for its competitive prices, they offer a range of equipment from top brands like Miller and Lincoln Electric.
- Welding Supplies From IOC: A reputable supplier for MIG, TIG, and Stick welding equipment along with high-quality safety gear.
- WeldingOutfitter.com: Offers an extensive selection of welding tools, accessories, and materials for professionals and amateurs alike.
- WeldingSupply.com: A broad range of welding machines, wire, and electrodes conveniently accessible online.
Understanding each retailer’s offerings ensures welders find supplies that match their specific project needs.
Tips for Finding Quality Products
When buying welding supplies online, consider the following tips to ensure quality:
- Read Reviews: Customer reviews provide insight into the performance and longevity of supplies.
- Check Return Policies: A clear and fair return policy protects buyers in case the product doesn’t meet expectations.
- Compare Prices: Don’t hesitate to compare prices across different platforms, but prioritize quality over the cheapest option.
- Look for Certifications: Ensure products meet industry standards and have appropriate certifications, providing peace of mind regarding quality.
Understanding Shipping and Returns Policies
For an uninterrupted shopping experience, familiarize yourself with the shipping and returns policies of online retailers:
- Shipping Costs: Consider the cost-effectiveness of shipping methods and whether the retailer offers free shipping above a certain order amount.
- Delivery Times: Be aware of expected delivery times and choose based on urgency; some suppliers offer expedited options.
- Returns Process: Understand how to initiate a return, including time limits and conditions for the return or exchange of products.
Knowledge of shipping and return procedures enhances the overall online shopping experience for welding supplies.
Best Practices for Using Welding Supplies
Implementing best practices for using welding supplies can significantly improve weld quality while minimizing damage and defects. Below are some effective strategies for optimally using equipment.
Proper Handling and Maintenance of Equipment
Maintaining welding supplies through proper handling and maintenance involves:
- Regularly Cleaning Equipment: Post-welding, clean all tools and equipment to prevent residue buildup.
- Storing Machines and Tools Properly: Keep equipment in designated areas to avoid accidental damage or misuse.
- Monitoring Consumables: Keep track of the usage levels of consumables like welding wire and electrodes to avoid unexpected interruptions in work.
- Calibration: Ensure welding machines are calibrated according to manufacturers’ recommendations.
These maintenance tasks help prolong the life of your equipment and ensure peak performance.
Maximizing the Lifespan of Your Welding Supplies
To extend the lifespan of welding supplies, consider the following strategies:
- Rotate Stock: Use supplies in the order they were purchased to minimize the risk of older supplies becoming obsolete.
- Proper Usage: Always follow best practices for settings based on material types and welding methods to avoid excess wear on machines.
- Effective Storage Solutions: Utilize climate-controlled storage for gases and sensitive items to protect from environmental extremes.
Focusing on effective management of welding supplies translates to better operational efficiency and cost savings.
Common Mistakes to Avoid
Many novice and even seasoned welders can make common blunders that impact the overall efficiency and quality of work. Some mistakes to avoid include:
- Neglecting Safety Gear: Skipping safety equipment can result in severe injuries; always prioritize protective gear.
- Overheating Materials: Excessive heat can warp materials; adjusting settings and techniques are crucial.
- Inconsistent Technique: Inconsistency in techniques can lead to poor weld quality; practice a uniform approach.
- Ignoring Equipment Maintenance: Failing to maintain equipment leads to performance issues and costly repairs.
Avoiding these missteps can significantly enhance both safety and quality in welding practices.
Trends in the Welding Supplies Market
The welding supplies market is constantly evolving with new technologies and methodologies. Below are some key trends that welders should be aware of.
Smart Technologies in Welding Equipment
Smart technologies are being integrated into welding equipment, providing enhanced functionality and ease of use. Features include:
- Digital Controls: Modern machines come equipped with digital interfaces, allowing for precise settings adjustments and adjustments from a mobile app or remote.
- Data Collection: Some advanced welders now incorporate sensors for monitoring and collecting data on performance metrics to optimize welding processes.
- Automated Welding Systems: These systems improve production efficiency by automating repetitive tasks while maintaining high-quality standards.
By embracing smart technologies, companies can enhance productivity and reduce the instance of human error.
Eco-Friendly Welding Supplies Innovations
The focus on sustainability and eco-friendliness has increased, prompting manufacturers to innovate. Some developments include:
- Alternative Energy Options: The rise of welding machines that use renewable sources of energy helps reduce environmental impact.
- Environmentally-Friendly Consumables: Manufacturers are producing low-fume welding consumables, reducing harmful emissions.
- Waste Reduction Efforts: Techniques and materials that minimize waste during the welding process are gaining prevalence.
These advancements not only enhance the eco-friendliness of welding practices but also align with global sustainability goals.
Industry Insights: What to Expect in the Future
The welding industry is evolving with expectations for further enhancements, including:
- Increased Demand for Skilled Welders: As technology advances, the need for skilled professionals who can operate advanced machinery will grow.
- Integration of AI and Robotics: AI-powered robotic systems are expected to take center stage, playing crucial roles in various welding applications.
- Customized Welding Solutions: Companies are looking more towards tailored welding solutions that cater to specific industry needs.
Staying informed about these trends allows both businesses and individual welders to adapt and thrive in a changing marketplace.