Leading Liquid Packaging Machine Supplier for Your Business Needs
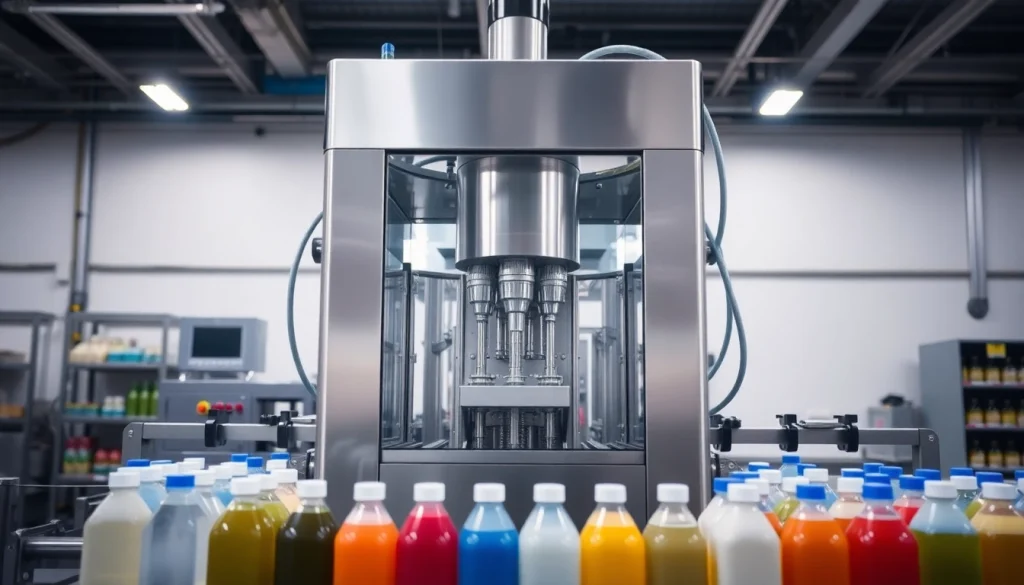
1. Understanding Liquid Packaging Machines
1.1 What are Liquid Packaging Machines?
Liquid packaging machines are specialized pieces of equipment designed to fill, seal, and package liquids into various containers, including bottles, pouches, and cartons. These machines play a critical role in ensuring the efficient handling of liquids across multiple industries, such as food and beverages, pharmaceuticals, cosmetics, and chemicals. With technology advancements, these machines can handle different viscosity levels, from water-like liquids to thicker pastes, thereby catering to a wide range of products.
1.2 Types of Liquid Packaging Machines
The world of liquid packaging machines encompasses various types tailored to specific applications and industries. Some of the most common types include:
- Filling Machines: These machines are used to fill containers with liquids at high speeds and precision. They include piston fillers, pump fillers, and gravity fillers, each suited for different liquid characteristics.
- Capping Machines: After filling, capping machines securely seal containers to protect products from contamination and spillage.
- Labelling Machines: These machines apply labels to filled containers to provide essential product information and branding.
- Palletizing Machines: Used for stacking filled and packaged products onto pallets for efficient transportation and storage.
1.3 Key Benefits of Using Liquid Packaging Solutions
Investing in liquid packaging solutions offers numerous advantages:
- Efficiency and Speed: Automated liquid packaging machines can significantly speed up the production process, decreasing labor costs and improving output.
- Consistency and Quality: These machines ensure uniformity in filling and sealing, reducing product wastage and ensuring quality control standards are met.
- Versatility: Liquid packaging machines can be designed to accommodate various container types and sizes, making them adaptable to different market needs.
- Enhanced Hygiene: Automated systems reduce human contact with products, thereby lowering the risk of contamination.
2. Choosing the Right Liquid Packaging Machine Supplier
2.1 Factors to Consider in a Supplier
When selecting a Liquid Packaging Machine Supplier, several factors should be evaluated to ensure a successful partnership:
- Experience and Expertise: Look for suppliers with a long-standing history and proven expertise in delivering reliable liquid packaging solutions.
- Reputation: Conduct thorough research to check customer reviews, industry recognition, and case studies to gauge the supplier’s reputation.
- Technological Advancement: The supplier should offer the latest technology and innovations in liquid packaging machinery, ensuring you stay ahead of the competition.
2.2 Evaluating Industry Experience and Reputation
Evaluate suppliers based on their industry experience. A supplier that specializes in your specific industry is more likely to understand your unique needs. Check for endorsements, certifications, and testimonials from past clients to assess their service quality. A reputable supplier will also provide references upon request, allowing prospective clients to gain insight into their operational integrity and after-sales service.
2.3 Customer Service and Support Assurance
Customer service and support are crucial components of a successful supplier relationship. Ensure that the supplier offers comprehensive support, including installation, training, and ongoing maintenance. A reliable supplier should also provide quick response times for any issues that may arise post-installation, ensuring minimal downtime and efficient operations.
3. Innovations in Liquid Packaging Technology
3.1 Automation and Smart Features
With advancements in technology, liquid packaging machines now feature automation and smart systems that enhance efficiency. These machines can integrate IoT (Internet of Things) technology, allowing operators to remotely monitor and control the packaging process. Automation reduces human error and optimizes productivity by precisely controlling filling speeds and minimizing product wastage. AI capabilities can also forecast maintenance needs, preventing unexpected breakdowns.
3.2 Sustainability in Packaging Solutions
As environmental considerations become more urgent, liquid packaging solutions are evolving to incorporate sustainable practices. Suppliers are increasingly focusing on eco-friendly materials, such as biodegradable films and recyclable containers. Implementing energy-efficient machines and reducing waste during the packaging process are also critical steps towards achieving sustainability in liquid packaging.
3.3 Customization Options for Diverse Industries
Each industry has specific requirements for packaging, which is why many suppliers offer customizable solutions. From modifiable machine sizes to unique filling processes, customization allows businesses in the food and beverage, pharmaceutical, and cosmetic industries to cater directly to their product’s needs. This adaptability not only enhances branding but also can offer better protection for the product and increase shelf life.
4. Best Practices for Liquid Packaging Operations
4.1 Efficiency in Production Lines
Maximizing efficiency in liquid packaging operations requires careful planning of production lines. Streamlining workflows involves coordinating between filling, capping, and labeling processes to minimize delays. Employing lean manufacturing principles can help identify and eliminate waste, thereby improving overall productivity. Additionally, regular audits and updates to machinery can enhance operational efficiency, ensuring that equipment meets production goals effectively.
4.2 Maintaining Equipment for Optimal Performance
Routine maintenance of liquid packaging machines is crucial for optimal performance. Developing a comprehensive maintenance schedule can help identify issues before they escalate. Regular checks on machine components, lubrication, and calibration ensure that your equipment operates smoothly. Establishing partnerships with suppliers for maintenance services can also facilitate quick repairs and replacements when necessary.
4.3 Training Staff on Liquid Packaging Systems
Investing in staff training is essential for the effective operation of liquid packaging machines. Comprehensive training programs should cover machine operation, safety protocols, and troubleshooting techniques. Regular refresher courses ensure that all employees remain up-to-date on the latest operating procedures and technologies, fostering a culture of safety and operational excellence within the workplace.
5. Case Studies: Successful Implementation of Liquid Packaging Solutions
5.1 Food and Beverage Industry Success Stories
Many companies in the food and beverage sector have successfully implemented liquid packaging machines to enhance their production efficiency. For instance, a major beverage manufacturer incorporated automated bottling lines to handle high-volume production, resulting in a 25% increase in output and a significant reduction in labor costs. By utilizing advanced filling technology, they improved accuracy while maintaining product quality standards.
5.2 Pharmaceutical Packaging Innovations
The pharmaceutical industry has seen breakthroughs in liquid packaging technology, particularly regarding compliance and safety. A leading pharmaceutical company adopted a comprehensive liquid filling line that integrated serialization technology for each container, ensuring traceability and compliance with global regulations. This implementation not only improved operational efficiency but also enhanced product security against counterfeiting.
5.3 Lessons Learned from Various Business Implementations
Evaluating case studies reveals valuable insights into the challenges and solutions in liquid packaging implementations. Companies often face hurdles such as machine downtime, compliance issues, and staffing shortages. However, lessons learned include the importance of regular maintenance schedules, continual staff training, and investing in adaptable technologies to meet changing market demands. These strategies have proven effective in achieving successful liquid packaging operations.