Leading Liquid Packaging Machine Supplier for Efficient Packaging Solutions
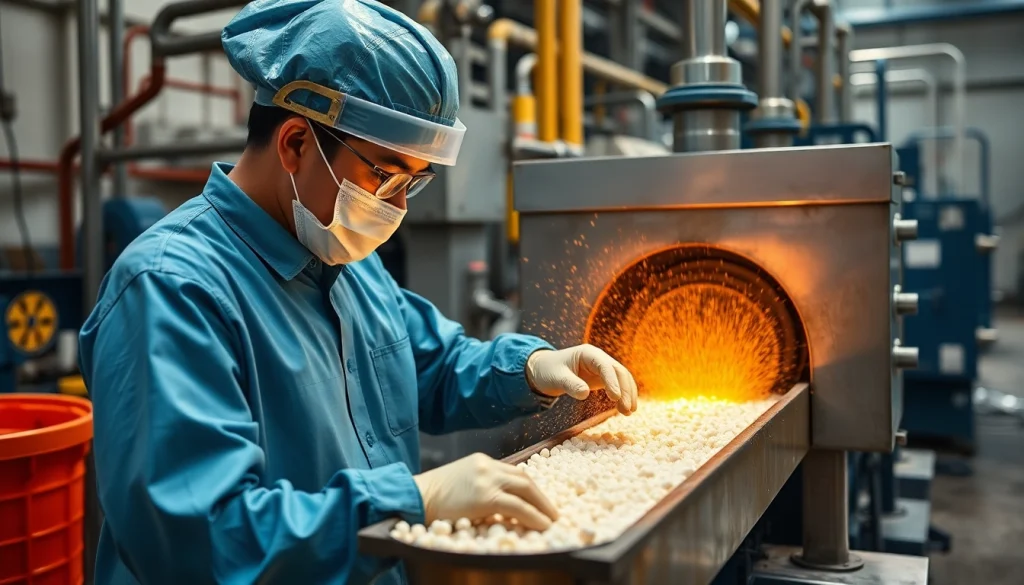
Introduction to Liquid Packaging Machines
In today’s fast-paced manufacturing landscape, the demand for efficient packaging solutions is ever-growing. One key component in this arena is the liquid packaging machine. These machines specialize in the automation of the packaging process for various liquid products, ensuring both efficiency and accuracy. Companies seeking to enhance their packaging capabilities often turn to a Liquid Packaging Machine Supplier to find the technology that best suits their needs. This comprehensive guide will delve deeper into liquid packaging machines, their importance, and how to choose the right supplier.
What is a Liquid Packaging Machine?
A liquid packaging machine is designed to package liquid products into containers, pouches, or bags. These machines can handle various liquids, including water, oils, sauces, creams, and more, making them versatile across multiple industries. The main functions of liquid packaging machines include filling, sealing, and sometimes even labeling, which streamlines the entire packaging process.
Importance in Various Industries
The significance of liquid packaging machines cannot be overstated, as they play a crucial role in several industries:
- Food and Beverage Industry: Provides effective and hygienic packaging for drinks, sauces, and perishable goods, extending shelf life while ensuring safety.
- Pharmaceutical Sector: Ensures precise dosing and tamper-proof packaging of medicines, which is vital for patient safety.
- Chemical Industry: Facilitates the safe filling and sealing of hazardous substances while adhering to regulatory standards.
- Cosmetics and Personal Care: Essential for packaging lotions, gels, and creams in an aesthetically appealing manner.
Types of Liquid Packaging Machines Available
Liquid packaging machines come in various types, each designed to cater to specific needs:
- Gravity Fillers: Utilize gravity to fill containers, ideal for low-viscosity liquids.
- Piston Fillers: Commonly used for thicker liquids; they use a piston mechanism to ensure accurate filling.
- Pump Fillers: Leverage pumps for liquids of varying viscosities, offering versatility.
- Vacuum Fillers: Use vacuum technology, minimizing air within the container, which is crucial for certain products.
- Form-Fill-Seal Machines: Integrate packaging production directly with the filling process, optimizing efficiency.
Choosing the Right Liquid Packaging Machine Supplier
When selecting a liquid packaging machine supplier, several factors must be considered to ensure you choose a partner that meets your operational needs.
Evaluating Supplier Capabilities
The first step in the supplier selection process is to evaluate their capabilities. Look for suppliers with a proven track record in your industry. They should offer machines that not only align with your specific needs but also possess advanced technology for automation and efficiency. Check if they provide customization options to tailor machines to your processes.
Key Considerations for Selection
Several key points should guide your selection process:
- Experience and Reputation: Assess how long the supplier has been in business and their reputation within the industry. Review testimonials and case studies from previous customers.
- Quality and Reliability: Research the quality of their machines – look for certifications and quality assurance processes. Reliability is crucial to avoid downtimes.
- Technological Advancements: Suppliers that invest in R&D to improve their packaging technologies can provide better machines addressing future trends.
- After-Sales Support: A good supplier provides comprehensive support post-purchase, including maintenance, parts supply, and technical assistance.
Customer Testimonials and Case Studies
Review relevant customer testimonials and case studies, as they offer insight into the performance and reliability of the machines in real-world settings. Engaging with existing customers or referencing documented success stories can help you gauge whether the supplier aligns with your business needs.
Technological Innovations in Liquid Packaging
Staying competitive requires keeping pace with technological innovations, particularly in liquid packaging, where advancements are continuous and significant.
Automation and Efficiency
The integration of automation in liquid packaging machines has significantly improved productivity. Automated systems reduce labor costs, minimize human error, and can operate continuously, allowing for higher output rates. Key trends include:
- Robotic Integration: Robots are increasingly used for sorting, packing, and palletizing, further enhancing operational workflows.
- Smart Technology: IoT-enabled machines can monitor performance in real-time, enabling predictive maintenance and minimizing downtime.
- Customizable Software Solutions: Advanced software allows for easy programming of various filling parameters, enhancing flexibility in production runs.
Eco-Friendly Packaging Solutions
Modern consumers demand sustainability, and liquid packaging suppliers are responding by investing in eco-friendly technologies. Ocean-friendly, recyclable bottles, and biodegradable pouches are increasingly popular. Best practices include:
- Material Innovation: Utilizing materials that reduce carbon footprints or are readily recyclable can promote sustainability.
- Reducing Packaging Waste: Adopting methods that minimize excess packaging, along with efficient design, can significantly reduce waste.
- Energy-Efficient Machines: Suppliers are focusing on energy-efficient machinery that consumes less power, contributing to a cleaner environment.
Trends Shaping the Future of Liquid Packaging
As industries continue to evolve, several trends are influencing the landscape of liquid packaging:
- Personalization: As consumer preferences shift, there is growing demand for personalized packaging solutions.
- Digital Printing: This enables brands to be more innovative with packaging design while enabling shorter production runs for customization.
- Health and Safety Considerations: Enhanced packaging solutions focused on minimizing contamination risk post-COVID-19 will drive innovation forward.
Common Applications for Liquid Packaging Machines
Liquid packaging machines are employed across a multitude of applications, demonstrating their versatility.
Food and Beverage Industry
In the food and beverage sector, filling and sealing machines cater to a variety of products, including:
- Sodas and Carbonated Beverages
- Juices and Health Drinks
- Cooking Oils and Sauces
These machines meet stringent health regulations and focus on preserving flavors and extending shelf life while maintaining consumer safety.
Pharmaceutical and Chemical Uses
Pharmaceutical manufacturing relies heavily on liquid packaging machines, specifically for:
- Liquid Medicines
- Vaccine Doses
- Chemical Solutions
These applications require high precision and compliance with safety regulations to ensure patient safety and product integrity.
Cosmetic and Personal Care Products
The cosmetics industry employs liquid packaging machines for a variety of personal care products, including:
- Lotions and Creams
- Shampoos and Conditioners
- Liquid Soaps
Design aesthetics, alongside functionality, are crucial in this industry, making distinctive packaging essential for market competitiveness.
Service and Support from Liquid Packaging Machine Suppliers
Choosing the right supplier is not solely about the machines they provide but also the support and services that accompany them. This is essential for long-term success.
After-Sales Service and Maintenance
A reputable liquid packaging machine supplier will offer robust after-sales services. Regular maintenance ensures machines operate optimally, preventing unexpected breakdowns that can disrupt production. This may include:
- Scheduled maintenance checks
- Quick response to technical issues
- Availability of spare parts and components
Customized Solutions and Consultation
Every business has unique packaging requirements. A supplier that provides tailored solutions can help you adjust your machinery to meet your specific needs. This could involve consultations to design packaging systems that enhance efficiency and efficacy.
Training for Optimal Machine Usage
Lastly, training is a critical aspect that many suppliers provide. Proper training ensures that your staff can operate the machines effectively and safely, optimizing productivity and minimizing the risk of accidents.