Enhancing Pipeline Integrity Through Expert Pipe Stress Analysis Company Insights
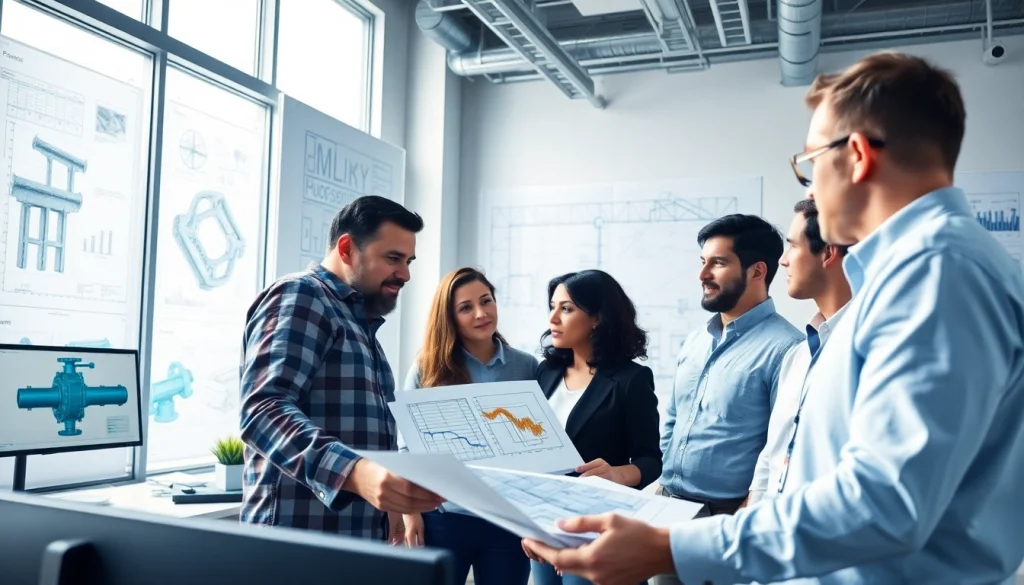
Understanding Pipe Stress Analysis Fundamentals
In the ever-evolving sectors of engineering and industrial operations, ensuring the integrity and reliability of piping systems is crucial. Pipe stress analysis forms the bedrock of this assurance. It involves assessing the physical stresses exerted on piping systems to prevent failures that could lead to catastrophic consequences. Companies specializing in this field become invaluable allies for businesses looking to enhance their engineering processes. A reputable pipe stress analysis company can leverage advanced technology and experienced professionals to assist in managing potential risks effectively.
What is Pipe Stress Analysis?
Pipe stress analysis is a systematic method used to determine the physical stresses and strains within piping systems. It involves evaluating various factors that exert forces on pipes, including internal pressure, external loads, thermal expansion, and weight. The analysis helps determine how these stresses can impact the integrity and functionality of pipelines, ensuring that they can withstand operational demands without failure.
Importance of Pipe Stress Analysis Company Services
Companies offering pipe stress analysis services play a pivotal role in various industries, including oil and gas, chemical processing, and water infrastructure. Their expert insights help in identifying potential failure points, compliance with regulatory standards, and optimizing design to enhance safety and efficiency. Investing in these services not only minimizes risk but also ensures longevity in infrastructure that is vital for operation.
Basic Principles of Stress Analysis for Piping Systems
The fundamentals of stress analysis encompass understanding material properties, load conditions, and the interaction of various forces acting on the pipes. Stress analysis begins by identifying the types of stresses in the system, including:
- Bending stress: Occurs when pipes are subjected to lateral forces.
- Tensile stress: Arises when a pipe is pulled in a linear direction.
- Compressive stress: Results from forces applied in a manner that compresses the pipe.
- Shear stress: Involves forces that cause slippage along a section.
Each of these stresses can significantly impact the lifetime and reliability of a piping system if not adequately addressed.
Common Challenges in Pipe Stress Analysis
Conducting an effective pipe stress analysis is not without its challenges. Several obstacles must be navigated to achieve reliable outcomes.
Identifying Stress Points in Pipelines
Understanding where stress concentrations occur is critical. Engineers must analyze factors like pipe supports, bends, and joints, which are common locations for stress accumulation. Utilizing Computer-Aided Design (CAD) software enhances the ability to visualize and simulate stresses in various configurations, facilitating a more accurate assessment.
Overcoming Design Limitations and Regulations
Piping systems often must adhere to stringent industry regulations and design limitations, which can complicate the analysis process. Engineers must ensure that their designs conform to codes such as ASME B31.3 for process piping or ASME B31.8 for gas transmission. Keeping abreast of these regulations while preserving the design intent requires comprehensive understanding and experience.
Managing External Factors Affecting Pipeline Stress
External conditions such as seismic activity, thermal expansion, and ground movement can induce unpredictable stresses in pipelines. Companies tendering pipe stress analysis need to account for these external variables during evaluations. Through environmental modeling and scenario analysis, experts can project the stresses pipelines may face under various conditions, thus preparing strategies for mitigation.
Best Practices for Effective Pipe Stress Analysis
To ensure high-quality outcomes in pipe stress management, various best practices can be integrated into operational protocols.
Utilizing Advanced Simulation Software
Modern simulation tools like ANSYS, CAESAR II, and AutoPIPE enhance the accuracy and efficiency of stress analysis. These applications enable engineers to model complex piping systems and predict stress responses under varying conditions and loads. Leveraging such technologies significantly reduces the likelihood of overlooking critical stress points during analysis.
Implementing Consistent Testing Standards
Establishing uniform testing and analysis standards is crucial for maintaining reliability in results. Recognizing the need for consistency, many how organizations adopt structured methodologies and practices guided by industry standards. Continuous adherence to these protocols ensures all personnel engage with a common understanding, leading to improved accuracy and safety outcomes in their analyses.
Continuous Training for Engineers in Pipe Stress Analysis
The field of pipe stress analysis is subject to rapid advancements in technology and methodologies. Continuous professional development programs for engineers facilitate knowledge upgrades, ensuring that teams remain at the forefront of industry practices. Formal training, workshops, and certifications can enhance skill sets, fostering a workforce equipped to tackle complex piping challenges effectively.
Case Studies: Successful Pipe Stress Management
Real-world applications of pipe stress analysis illustrate its benefits and potential for increasing operational efficacy. The following case studies provide insight into various industries effectively managing pipeline stress.
Case Study 1: Mitigating Risks in Oil & Gas Pipelines
A leading oil and gas company faced challenges with the integrity of its pipeline systems across multiple sites. By engaging a professional pipe stress analysis company, they implemented comprehensive stress analyses using advanced simulation tools. The company identified critical stress points that required reinforcements and optimized support placement, resulting in reduced risk of pipeline failures and enhanced operational longevity.
Case Study 2: Innovations in Chemical Processing Systems
In the chemical industry, a manufacturer experienced frequent downtimes due to unexpected failures in its piping systems. A detailed stress analysis revealed inefficiencies in their piping network, particularly around connections and bends. By redesigning the piping layout and employing proper support techniques highlighted through the analysis, the manufacturer experienced significant reductions in downtime and an improvement in overall production capacity.
Case Study 3: Improving Reliability of Water Infrastructure
A municipal water utility faced challenges with aging infrastructure leading to frequent leaks and breaks. By contracting a specialized pipe stress analysis firm, they conducted extensive assessments of the existing systems. The findings directed necessary upgrades, including the replacement of critical sections and enhancements in support structures. As a result, the utility saw a marked decrease in incidents, improving the overall reliability of water distribution.
Measuring Success in Pipe Stress Analysis Projects
Success in pipe stress analysis is quantifiable through established metrics that define effective management and operational improvements.
Key Performance Indicators (KPIs) for Pipe Stress Analysis
Organizations often rely on KPIs to gauge the efficacy of their pipe stress analysis initiatives. Common KPIs might include:
- Reduction in pipeline failures
- Cost savings due to improved design efficiency
- Time saved during analysis and design phases
- Enhanced compliance with regulatory standards
Monitoring these KPIs helps organizations identify areas for improvement and validate the return on investment of their pipe stress analysis efforts.
Monitoring and Reporting Techniques
Effective monitoring employs sophisticated techniques that compile, analyze, and report data throughout the pipe stress analysis life cycle. Utilizing dashboards and progress reports helps stakeholders remain informed about ongoing projects, outcomes of analyses, and any necessary adjustments in strategy. Regular updates allow for timely interventions when potential issues are identified.
Integrating Feedback for Continuous Improvement
Collecting feedback from the implementation stages of pipe stress analysis projects is essential for continuous improvement. By encouraging open dialogues among engineers and stakeholders, companies can gather valuable insights that foster adaptations and refinements in their approach. Incorporating lessons learned ensures ongoing developments that align with best practices and industry standards.