Enhancing Performance with Expert Pipe Stress Analysis from an Industry Leader
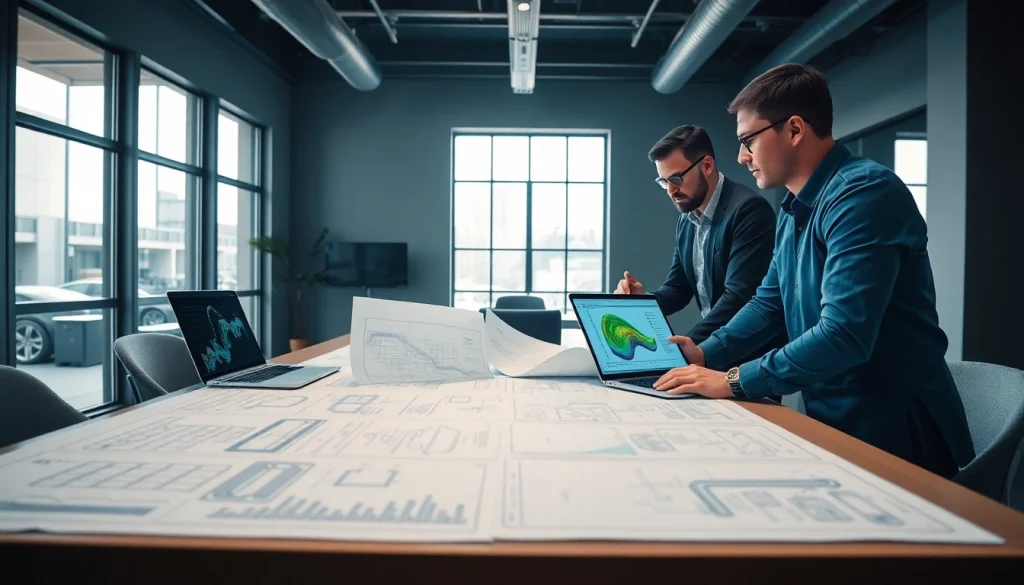
Understanding Pipe Stress Analysis
What is Pipe Stress Analysis?
Pipe stress analysis is a critical engineering process that evaluates the structural integrity and performance of piping systems under various loads and conditions. In industries involving fluid transport, such as oil and gas, chemicals, and nuclear power, understanding how pipes will behave under operational stresses is essential for ensuring safety and reliability. The analysis encompasses several factors including thermal expansion, wind and seismic loads, pressure changes, and other dynamic forces that might affect a pipeline during its lifecycle.
The ultimate goal of pipe stress analysis is to identify potential failures or weaknesses before they occur, helping organizations to mitigate risks and optimize the design of their systems. Engaging a pipe stress analysis company can provide the expertise and tools necessary for thorough assessments and effective solutions.
Importance of Accurate Assessments
Accurate assessments in pipe stress analysis are paramount. Inaccuracies can lead to serious consequences such as leaks, explosions, and system failures that not only result in financial losses but also pose significant risks to life and the environment. For example, a faulty analysis might overlook the stresses caused by temperature variations which can lead to cracking in materials or joint failures. Additionally, complying with industry standards and regulations necessitates rigorous testing and validation of piping systems.
Regular and precise evaluations can extend the lifespan of piping systems, minimize maintenance costs, and improve overall operational efficiency. By proactively addressing the potential for stress-related issues, organizations can not only safeguard their workforce and the surrounding community but also enhance their reputation in the market.
Common Methods Used in the Industry
The industry employs various methods for conducting pipe stress analysis, and selecting the right approach depends on the specific requirements of the application. Some of the common techniques include:
- Finite Element Analysis (FEA): This computational technique breaks down complex piping systems into smaller, manageable finite elements, allowing engineers to assess stress distribution and deformation accurately.
- CAESAR II Software: A leading software tool specifically designed for pipe stress analysis that incorporates various design codes and standards, enabling efficient and reliable analysis.
- Bending Moment and Shear Force Analysis: This method focuses on evaluating the forces acting on bends and joints, providing insights into potential failure points.
- Thermal Expansion Analysis: Important for systems where temperature fluctuations are expected, focusing on how materials expand or contract in response to heat.
Key Applications of Pipe Stress Analysis
Pipeline Design and Integrity
One of the primary applications of pipe stress analysis is in the design phase of pipelines. Engineers can ensure that piping systems are constructed to withstand expected stresses and pressures throughout their operational life. This involves simulating various scenarios and assessing numerous variables that impact performance. For instance, in high-temperature applications, the thermal properties of materials must be thoroughly understood and analyzed.
Additionally, integrity assessments through stress analysis play a crucial role in maintaining the overall health of pipelines. Regularly scheduled evaluations can detect early signs of fatigue or damage, allowing organizations to take corrective action before smaller problems escalate into significant failures.
Maintenance Strategies for Industrial Pipelines
Incorporating pipe stress analysis into maintenance strategies can lead to more effective and efficient practices. Traditional maintenance often relies on fixed schedules without adequately assessing the actual conditions of the pipelines. However, integrating analysis into maintenance practices allows for condition-based assessments that can optimize maintenance operations based on real-time data and actual stresses experienced by the pipeline.
For instance, advanced monitoring systems can provide real-time data regarding temperature, pressure, and flow, which can then be used to perform ongoing stress analyses. This ensures that any necessary maintenance or repairs are conducted proactively, minimizing downtime and extending the lifespan of the pipeline.
Risk Assessment and Safety Compliance
Risk assessment is another critical application of pipe stress analysis. By evaluating potential failure modes and their impacts, organizations can implement robust safety measures to protect their personnel and the environment. This is particularly important in industries that handle hazardous materials, where the consequences of a pipeline failure can be catastrophic.
Moreover, ensuring compliance with local and international regulations surrounding pipe safety often requires detailed documentation of stress analyses and the measures taken to mitigate risks. This not only helps to meet legal obligations but also demonstrates a company’s commitment to safety and reliability.
Best Practices for Pipe Stress Analysis
Selecting the Right Tools and Software
The choice of tools and software for pipe stress analysis can significantly impact the quality of the assessments conducted. Organizations should opt for specialized software that is regularly updated to align with changing industry standards. Tools like CAESAR II, AutoPIPE, and Simulia are widely recognized for their capabilities in handling complex pipe stress analysis.
In addition to software, engineers should also harness supporting tools such as CAD systems and simulation software to visualize the piping systems in three dimensions. This holistic approach can improve accuracy and provide deeper insights into potential stress-induced failures.
Integrating Analysis with Design Processes
Integrating pipe stress analysis early in the design process is vital for achieving optimal results. By involving stress analysis in the initial stages, engineers can identify and mitigate potential issues before construction begins. This proactive approach reduces the likelihood of costly reworks and enhances the overall design quality.
During this integration, it is advisable to create iterative feedback loops where analysis results inform design modifications and vice versa. By continually assessing the implications of design changes through stress analysis, teams can implement more effective solutions from the outset.
Collaborating Across Engineering Disciplines
Successful pipe stress analysis requires collaboration among various engineering disciplines, including mechanical, civil, and structural engineering. Through interdisciplinary communication and teamwork, organizations can ensure that all factors influencing pipe performance are considered. For instance, input from structural engineers can provide valuable insights on the support structures that will affect the piping system’s load-bearing capability.
Additionally, collaboration with safety and environmental engineers further enhances the integrity of the analysis, as they can offer perspectives on potential risk factors and compliance requirements. Establishing a culture of cross-discipline collaboration encourages innovation and leads to more resilient engineering outcomes.
Challenges in Pipe Stress Analysis
Addressing Miscalculations and Errors
Despite advancements in analysis tools and methods, miscalculations and errors remain a significant hurdle in pipe stress analysis. Mistakes can arise from various sources such as incorrect material properties, inadequate modeling techniques, or changes in operating conditions that are not taken into account. Inaccuracies can result in design flaws that lead to severe operational failures.
To mitigate these risks, organizations should implement rigorous verification and validation processes for their analysis results. This may include peer reviews, automated tests against known benchmarks, and validation against real-world performance data where available. Developing a robust protocol for quality assurance can greatly enhance the credibility of pipe stress analysis outcomes.
Environmental and External Impact Considerations
When conducting pipe stress analysis, it is vital to consider external factors such as environmental conditions. Temperature variations, ground movements, and seismic events can impose significant unforeseen stresses on piping systems. Furthermore, changes in external loads due to additional infrastructure or natural disasters should also be examined.
In order to address these challenges, engineers should stay informed about local geological and meteorological conditions that could affect the long-term performance of piping systems. Conducting thorough environmental impact assessments as part of the stress analysis can lead to more comprehensive understanding and effective design adjustments.
Staying Updated with Industry Standards
The field of pipe stress analysis is constantly evolving, with changes to technology, methodologies, and regulatory requirements. Staying updated with industry best practices and standards is crucial for maintaining compliance and ensuring high levels of safety and reliability. Organizations must regularly participate in industry conferences, training programs, and review the latest publications to keep abreast of advancements.
Additionally, developing partnerships with academic institutions and industry groups can further enhance knowledge sharing and keep practitioners informed on the latest research and innovations in piping systems and analysis techniques.
Future Trends in Pipe Stress Analysis
Advancements in Technology and Software
The future of pipe stress analysis will be heavily influenced by technological advancements. As computational power continues to increase, the complexity of simulations and analyses will expand correspondingly. New algorithms and software tools are being developed to enhance the accuracy and speed of assessments, which will allow engineers to make more informed decisions in real-time.
Moreover, the integration of cloud computing and big data analytics enables engineers to process vast amounts of operational data for predictive maintenance purposes. Enhanced simulation capabilities mean that organizations will be better equipped to foresee and mitigate potential risks associated with stress conditions in their piping systems.
Emphasis on Sustainable Engineering Practices
In recent years, there has been a growing emphasis on sustainability within engineering practices, and pipe stress analysis is no exception. More organizations are adopting green engineering principles, focusing on minimizing material use, reducing waste, and designing systems that are energy efficient. This shift requires engineers to analyze the environmental impact of their designs and implement solutions that align with sustainability standards.
As regulations become stricter regarding environmental protection, organizations that prioritize sustainability in their pipe stress analysis will likely have a competitive edge in the marketplace. Implementing sustainable practices ensures compliance while also appealing to environmentally conscious consumers and stakeholders.
The Role of Automation and AI in Analysis
One of the most exciting trends in pipe stress analysis is the increasing use of automation and artificial intelligence (AI). These technologies can significantly enhance the speed and accuracy of analyses by automating repetitive tasks and enabling more complex calculations. AI-driven predictive maintenance tools can analyze historical data to forecast potential failures and inform maintenance scheduling seamlessly.
As more advanced algorithms are developed, we can anticipate a future where real-time analysis and reporting become the standard practice, providing organizations with immediate insights into the performance of their piping systems. This not only improves efficiency but also empowers engineers to make proactive decisions to optimize system integrity continually.